Industrial welding robots are transforming production lines by delivering exceptional efficiency. Amid rising material costs and global labor shortages, businesses require optimal solutions to stay competitive. Welding, a vital process, is greatly enhanced by welding robots, which boost productivity, ensure precision, and cut costs. These robots are highly adaptable, supporting techniques like arc welding, resistance welding, and spot welding, resulting in uniform products with minimal defects. In Vietnam, with its fast-growing economy, welding robots are an inevitable trend, aiding in the production of automobiles, motorcycles, furniture, and supermarket shelves while saving labor and improving quality.
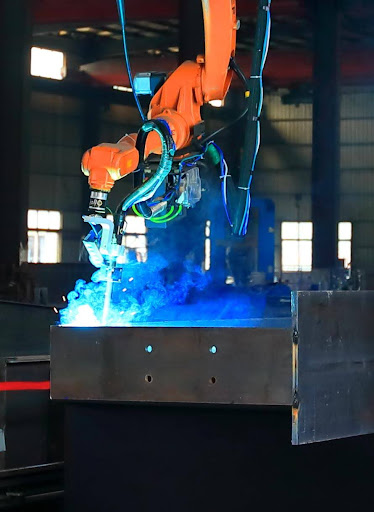
1. What is a Welding Robot?
An industrial welding robot is an automated solution for welding processes, improving precision, safety, and time efficiency while effectively replacing traditional manual methods. Capable of adapting to diverse techniques such as arc welding, resistance welding, and spot welding, these robots produce consistent, high-quality products with fewer errors. They are widely used in manufacturing car frames, motorcycles, railings, gates, school furniture, and supermarket shelves. In Vietnam’s developing economy, especially with post-COVID-19 labor shortages, welding robots are a necessary trend, enabling businesses to save labor, increase productivity, and maintain product quality.
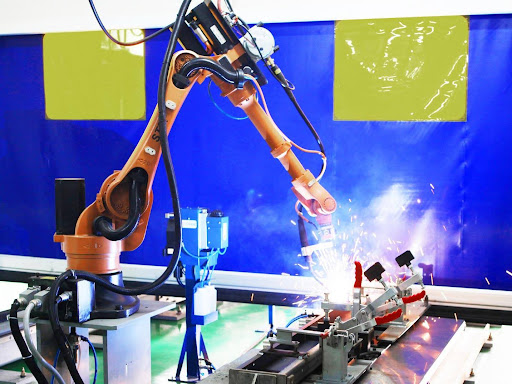
2. Outstanding Benefits of Using Robots in Welding Applications
Using robots in welding brings significant advantages to the manufacturing industry. Here are the key benefits:
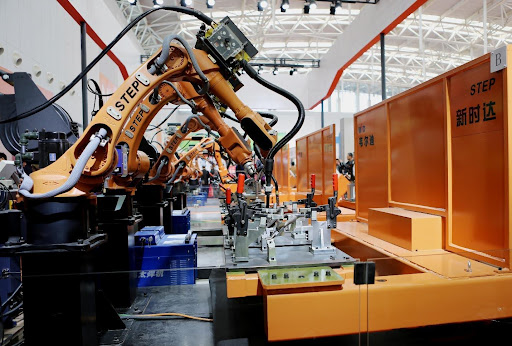
Increased Precision and Weld Quality
Welding robots are programmed to execute precise, uniform welds, ensuring top-tier product quality. This is particularly valuable in industries like automotive, aerospace, and electronics, where accuracy is paramount.
Enhanced Productivity
Operating continuously 24/7 without breaks, robots significantly outperform manual welding in productivity. They also handle complex welds quickly and efficiently.
Reduced Labor Costs
By decreasing dependence on manual labor, welding robot lower expenses related to wages, training, and benefits.
Improved Workplace Safety
Manual welding involves risks like high heat, sparks, and toxic fumes. Robots eliminate these hazards, safeguarding workers’ health.
Application Flexibility
Programmable for various welding methods (e.g., arc, spot, resistance welding), robots adapt easily to changing production demands.
Reduced Material Waste
High precision minimizes material waste, reducing costs and supporting environmental sustainability.
Seamless Production Line Integration
Welding robots integrate effortlessly into automated systems, streamlining processes and boosting overall efficiency.
Remote Monitoring and Maintenance
Modern welding robots offer remote monitoring and maintenance capabilities, simplifying performance management and upkeep.
Increased Competitiveness
Higher product quality, lower costs, and faster market responsiveness give businesses a competitive edge.
Skill Development Opportunities
Robots enable workers to learn advanced skills like programming, operation, and maintenance, moving beyond manual tasks.
In summary, welding robots enhance production efficiency, safety, and flexibility while reducing costs, making them indispensable in modern industry.
3. How Are Welding Robots Practically Applied in Industry?
Welding robots are critical in modern manufacturing, delivering practical benefits across various sectors. Below are key real-world applications:
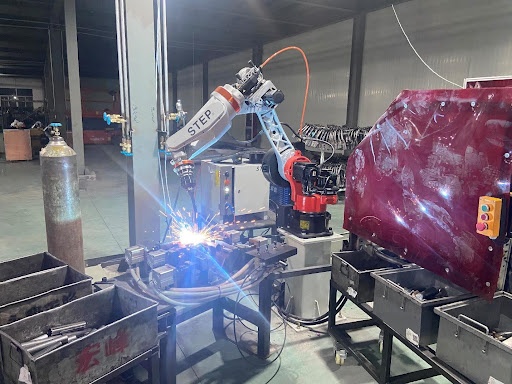
3.1. Automotive Industry
Welding Car Frames: Robots assemble metal car frame components with precision and durability. For instance, Toyota factories use robots for complex welds on car bodies, accelerating production and minimizing errors.
Welding Small Parts: Spot welding robots assemble doors, hoods, and interiors, ensuring consistency and quality.
3.2. Aerospace Industry
Welding Aircraft Parts: Robots weld special alloys like titanium and aluminum, ensuring flawless precision for critical components like wings and fuselages.
Welding Satellites and Rockets: Arc welding robots craft intricate satellite and rocket structures, where strength and accuracy are essential.
3.3. Electronics Industry
Welding Circuit Boards: Robots perform micro-welds on circuit boards, ensuring accurate connections and reducing errors in mass production.
Welding Electronic Components: In devices like smartphones and computers, robots assemble tiny parts quickly and reliably.
3.4. Shipbuilding Industry
Welding Ship Hulls: Robots weld large metal plates for ship hulls, cutting production time and ensuring watertightness.
Welding Internal Structures: Robots navigate pipelines and complex interiors, delivering long, high-quality welds.
3.5. Furniture and Metal Structure Manufacturing
Welding Furniture Frames: Robots produce metal furniture with precision, ensuring uniformity and aesthetics.
Welding Railings and Gates: Programmed for intricate details, robots enhance the durability and beauty of railings, stairs, and gates.
3.6 Home Appliance Manufacturing
Welding Washing Machine and Refrigerator Parts: Robots weld appliance components, ensuring durability and safety.
Benefits of Welding Robots in Production Welding robots elevate production through:
Increased Productivity: Continuous operation speeds up manufacturing timelines.
High Precision: Reduced errors ensure consistent quality.
Improved Safety: Workers are protected from welding hazards.
Cost Savings: Lower labor and material costs optimize efficiency.
Real-World Examples
Tesla: At its Gigafactory, Tesla deploys hundreds of welding robots to assemble electric car bodies, achieving high-quality mass production rapidly.
Boeing: Boeing uses welding robots for complex aircraft welds, ensuring safety and durability.
Welding robots are integral to modern manufacturing, from automotive to electronics and beyond. By boosting productivity, quality, and safety, they meet market demands and pave the way for future innovations.
Leave a Reply